All boilers are subject to damage if proper chemical treatment, water analysis and blowdown procedures are not followed. If these items are ignored, both during operation and idle periods, serious damage to the boiler will result.
When Nationwide Boiler delivers a rental unit, it is the boiler operator's responsibility to maintain and supervise the water treatment conditions of their rental boiler in order to avoid any additional charges that may result from improper operation or maintenance. It is recommended that the services of a reputable boiler chemical consultant are retained in-order to supervise the water treatment conditions on a regular basis. At least once each week, daily boiler logs, chemical treatment tests, a chemical treatment consultant's report and maintenance records should be implemented and sent to Nationwide Boiler. This ensures that the proper maintenance is being done on the equipment and provides accurate maintenance reports for Nationwide's equipment files.
As a boiler operator it is important to inspect the waterside condition of watertube boilers that may result in heavy scale or oxygen pitting or corrosion. Waterside scale can be cause for concern on the reliability of a boiler by the following:
Oxygen corrosion is not as easily detected as scale. O2 pitting can occur under deposits and in very small areas that can escape detection by the naked eye. If O2 pitting is suspected, a tube needs to be removed from the boiler for more close examination.
Therefore, it is extremely important to assess the waterside condition of a boiler and then to determine the type of scale and the method for removing it. There are several methods for removing boiler scale including high pressure water blasting and other proprietary methods offered by water treatment representatives. Overall, with proper boiler maintenance and water treatment plans, such procedures can be avoided.
Examples of (1) Heavy Scale, (2) Medium Scale and (3) No Scale
1.
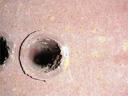
2.
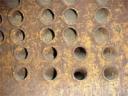
3.
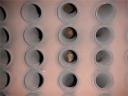
When Nationwide Boiler delivers a rental unit, it is the boiler operator's responsibility to maintain and supervise the water treatment conditions of their rental boiler in order to avoid any additional charges that may result from improper operation or maintenance. It is recommended that the services of a reputable boiler chemical consultant are retained in-order to supervise the water treatment conditions on a regular basis. At least once each week, daily boiler logs, chemical treatment tests, a chemical treatment consultant's report and maintenance records should be implemented and sent to Nationwide Boiler. This ensures that the proper maintenance is being done on the equipment and provides accurate maintenance reports for Nationwide's equipment files.
As a boiler operator it is important to inspect the waterside condition of watertube boilers that may result in heavy scale or oxygen pitting or corrosion. Waterside scale can be cause for concern on the reliability of a boiler by the following:
- If the boiler tubes contain heavy scale, tubes can overheat and/or fail leading to tube leaks
- If the boiler has some scale but it is not heavily deposited, certain types of water treatment plans can cause the scale to quickly be removed in large flakes, plugging tubes and eventually leading to overheating and tube failures
- Certain types of scale can be easily removed such as a conventional soft phosphate scale, while others are very difficult to remove such as silica
Oxygen corrosion is not as easily detected as scale. O2 pitting can occur under deposits and in very small areas that can escape detection by the naked eye. If O2 pitting is suspected, a tube needs to be removed from the boiler for more close examination.
Therefore, it is extremely important to assess the waterside condition of a boiler and then to determine the type of scale and the method for removing it. There are several methods for removing boiler scale including high pressure water blasting and other proprietary methods offered by water treatment representatives. Overall, with proper boiler maintenance and water treatment plans, such procedures can be avoided.
Examples of (1) Heavy Scale, (2) Medium Scale and (3) No Scale
1.
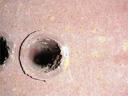
2.
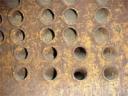
3.
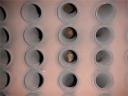
8728 Hits